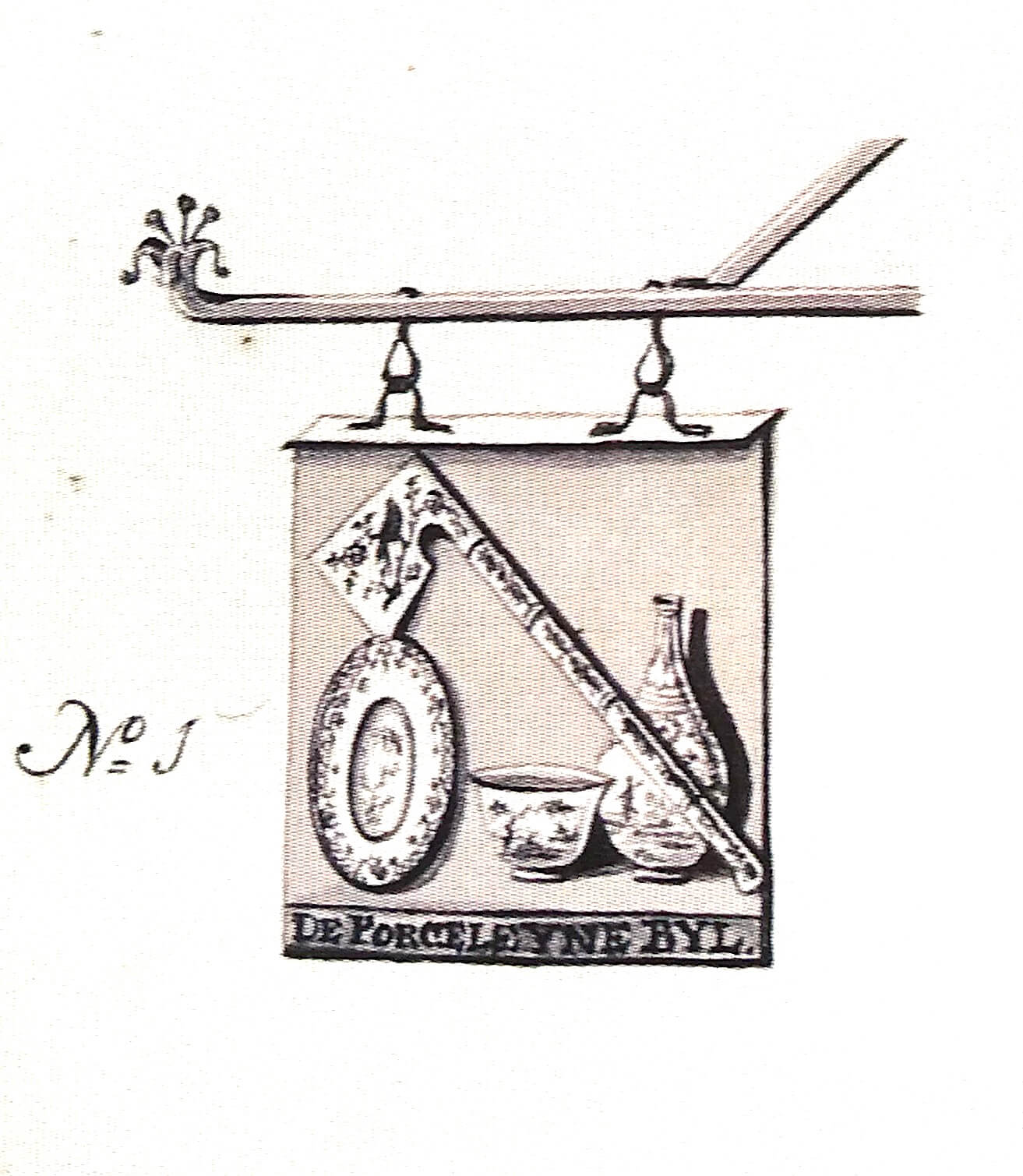
The Rise and Fall of the Delft Potteries
During the sixteenth century, The Delft economy was driven by the textile industry and beer breweries. However, the combination of these two industries caused problems. The textile industry polluted the water, which was an essential ingredient for beer. Therefore, the city of Delft needed a new industry to stimulate the economy, what eventually became the earthenware industry. The Delft earthenware industry grew extensively in the seventeenth and eighteenth centuries, and formed the backbone of the urban economy.
At the end of the sixteenth century, several majolica potters and painters were established in Delft, Haarlem, Amsterdam, Rotterdam and Makkum. Of these cities, Delft was the most successful in the earthenware industry, because the potters and painters imitated the popular Chinese porcelain. Majolica potters were primarily from the Southern Netherlands, and fled the region after the Spanish war.
In 1640, Delft had eleven potteries, each with probably one kiln, and an average of fifteen painters and servants.[1] After civil unrests in China (1644-1647), the importation of Chinese porcelain stagnated, from 200,000 pieces to 125,000 pieces in 1647, and only a mere 15,000 pieces in 1652. With this rapid decline, the Delftware industry captured a large market share during the second half of the seventeenth century.[2] The number of factories increased to 28 in 1670, and many factories were equipped with a second kiln.[3] De Porceleyne Schotel (The Porcelain Dish) factory even had three kilns, according to a fire inspection in 1668.[4] At its peak, the number of Delftware factories grew to more than thirty around 1700.[5] To fill these kilns, the production and number of employees must have been increased. Since no official number is known, the estimates of employees working in one factory vary from fifteen to sixty. The Hedendaagsche historie mentions approximately thirty people per kiln.[6]
Delftware factories were complex production houses that employed specialized workers. These factories far surpassed the traditional notion of a craft industry with a master and his workshop. A factory was comprised of a workshop and a kiln, warehouses, attics for hay and for objects to dry, a house to live and a shop. Further, one had to have a so-called ‘aardewasserij’ (a place to clean the earth), a paint mill and a kiln for tin ashes. Since most of the production was done in the factory, many materials and hands were needed. As a document from 1748 states: ‘onse fabriek is overeenkomstig met een horologie, daar wanneer een rad ontbreekt alle de anderen stil staan’ (our factory is like a timepiece, because if one wheel stops, all the others come to a halt).[7] The multitude of tasks in the factory imposed high organizational demands and increased the operating costs.
Membership of the Guild of Saint Luke was required for a potter or painter to manage his own factory. After acquiring this mastery, he could appoint servants and students to work for him. Painters formed the majority of the employees, followed by the throwers. There was no limit to the number of servants that a master potter could employ, and sometimes these contracts lasted for many years. For example, Lambertus van Eenhoorn contracted a ‘stoker’ for 25 years.[8] A master could also employ two students in addition to the servants. If more than two students where appointed at once, the owner was issued a fine of 12 guilders. This rule, which was not always closely met, was established in 1614 to prevent the concentration of the craftsmanship in large factories. The rule also protected the ordinary servants from being replaced by cheaper student labor.[9] This, however, also had its drawbacks. In years of strong industry growth, the rule halted staff growth during busy periods. Further, masters were allowed to employ their sons as factory apprentices in addition to the two students.
The pottery industry in Delft did not continuously flourish during the seventeenth and eighteenth centuries. The first years of the eighteenth century were laborious, partly due to the outbreak of the Spanish succession war (1702-1713). In 1748 the Delft potters stated that 1702 was the worst year to date.[10] This suggests that between 1702 and 1748 there was a recovery, and although there was a decline in the number of factories, there were still over twenty factories in operation in Delft.[11]
There was increased competition over the course of the eighteenth century due to a number of factors. Price fixing and a compulsory winter closure had to counteract price competition and overproduction. Due to falling prices of Chinese and Japanese porcelain, and later the importation of the harder and cheaper English creamware, the demand for Delftware decreased.[12] In addition, France, the Southern Netherlands and especially England began to protect their own growing pottery industries, which caused a decline of the Delftware export market.[13] Although the Delft potters found a new source of inspiration in Western earthenware and porcelain, the quality of their objects either remained the same or declined. Some factories were forced to sacrifice the quality of their earthenware in order to lower prices and compete with other products. This worried the former Delftware producer Gerrit Paape, who complained of poor quality, dull, colorless paintwork and a stubborn adherence to oriental styles, executed in a particularly clumsy way in his treatise De Plateelbakker of Delftsch aardewerkmaaker from 1794.[14]
While some factories achieved success in spite of these setbacks, the sale of Delftware decreased and many factories had to scale back production. More and more Delft producers were forced out of business; at the end of the century, a mere eleven factories remained in operation. After the French period (1795-1813), the pottery industry did not revitalize and the only remaining factory was De Porceleyne Fles (The Porcelain Bottle).[15]
Notes
[1] M.S. van Aken-Fehmers, L.A. Schledorn, A.- G. Hesselink, T.M. Eliëns, Delfts aardewerk. Geschiedenis van een nationaal product, Volume II, Zwolle/Den Haag (Gemeentemuseum) 1999, p. 38.
[2] Van Aken-Femers 1999 (note 1), p. 38.
[3] Van Aken-Femers 1999 (note 1), p. 38.
[4] Loet Schledorn, ‘Delftse plateelbakkers in het Lucasgilde’ in Holland: regionaal-historisch tijdschrift, vol. 36 (2004), afl. 2, pag. 83-96, p. 87.
[5] Schledorn 2004 (note 4), p. 87.
[6] Hedendaagsche historie, of tegenwoordige staat van alle volkeren enz., Van Aken-Femers 2001 (note 1), p. 41.
[7] M.S. van Aken-Fehmers, Het wonder van Delftsblauw / DelftWare WonderWare, Den Haag/Zwolle, 2012, p. 10.
[8] Van Aken-Femers 1999 (note 1), p. 42.
[9] Schledorn 2004, p. 90.
[10] Bergvelt, Jonker, Wiechman (red.), Schatten in Delft. Burgers verzamelen 1600-1750, Zwolle/Delft (Stedelijk Museum Het Prinsenhof) 2002, p. 153.
[11] Bergvelt 2002 (note 10), p. 153.
[12] Bergvelt 2002 (note 10), p. 153.
[13] Van Aken-Femers 2001 (note 1), p. 38.
[14] G. Paape, De Plateelbakker of Delftsch Aardewerkmaaker, Dordrecht 1794; herdruk Amsterdam 1978, pp. 28-29.
[15] Van Aken-Femers 1999 (note 1), p. 38.